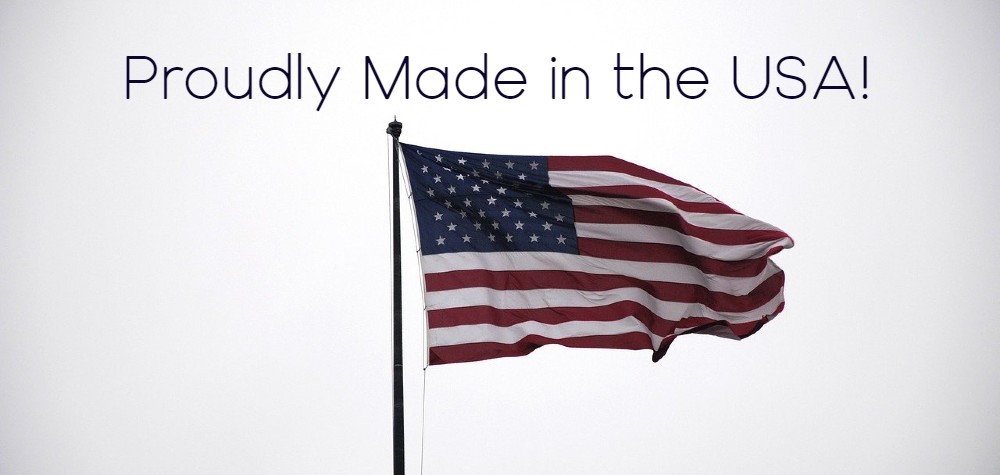
I have a great story. Actually, we have lots of them, but this one stands out in my memory.
We recently purchased some used twisting equipment from a mill in North Carolina. Now, recall if you will, that until the mid-90’s, there were tens of thousands of textile jobs in the area of western North Carolina. Then, for a variety of reasons, those jobs went overseas, devastating that part of the Country. Truly a terrible situation, but I’ll stay out of the politics and economics of the whole thing.
Anyway, we bought several twister frames from a broker. They came out of a mill that was shut down. We brought them up to Northern NY to add to our existing operation that twists very high temperature threads, yarns, and other products. The drivers and riggers that delivered these frames were all quick to point out how great it was that they didn’t deliver them to some port on the east coast to ship out on a freighter to another country. Rather, this time, those twister frames were actually going to a new industrial building in Upstate N.Y., USA! What a great feeling for all of us here at W.F. Lake Corp.! Working together, we were all investing in the future of the United States of America!
W.F. Lake Corp. manufactures all of its products in the U.S.A. and we’re proud of it. Since our founding in 1991, we’ve been especially aware of the need to produce products here at home. We’re fortunate to have been born here and we appreciate it!
It’s interesting to take a look at how important it is to have manufacturers here and to support them when you can. We like to point out that when it comes from the US, the box it came in was likely made in the US, the poly bag in the box, the truck driver that delivered the materials lives here, the guy repairing the truck, the company that put up the building, filled the vending machine, cleans the carpets, plows the driveway… well, you get the idea.
Statistics abound as to how important manufacturing is to the US Economy and I’ll spare you the details, save one. The highest multiplier effect of any economic sector in the US is manufacturing. Don’t forget the person at the bakery who bakes the cake for “birthday month” and makes the buns for the hot dogs for the impromptu “bosses turn to cook” cookout, and… Sorry, got carried away again.
Made in the U.S.A. matters and we’re proud to say that is what we do!
Send us a note to find out more about what we do and the products we offer!